Life Style
Laser Welding Aluminum: A Comprehensive Buyer’s Guide
Published
9 months agoon
By
Prime Star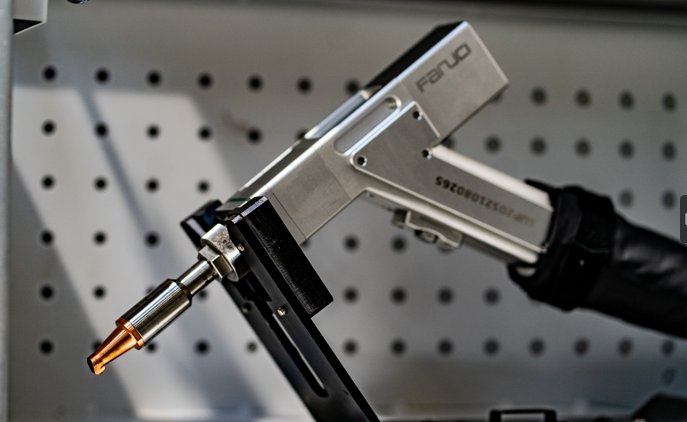
Aluminum is gradually replacing other construction materials in various sectors owing to its lightweight, non-corrosive, high strength-to-weight ratio, and ease of recycling. As aluminum’s application increases, the techniques for connecting aluminum components are significant. Laser welding is one of the more highly developed technologies for joining aluminum.
Laser welding involves focusing a high-powered laser beam on a specific region to cause melting and joining of the target materials. Due to the nature of laser welding, which offers exact cuts and clean edges, it is an ideal method of welding aluminum. Aluminum laser welding has more advantages compared to other conventional welding techniques.
However, choosing the right laser welding technology suitable for aluminum applications takes a lot of work. The purpose of this buyer’s guide is to provide you with all the necessary information regarding laser welding aluminum. Here we provide information on some essential factors to consider in laser welding, the various processes of laser welding, and the best practices when purchasing equipment to suit your needs in laser welding aluminum.
The main factors to consider when welding aluminum using laser welding techniques are the following.
Some key factors to consider when selecting an aluminum laser welding system include Some key factors to weigh when selecting an aluminum laser welding system include:
Joint Type
Laser welding of aluminum can be done in lap joints, butt joints, filet joints, and wire seams. Evaluate the types of joints you want to manufacture and choose a laser to create appropriate weld profiles. Butt joints may need more precise positioning equipment and fixtures as compared to the other joints.
Material Type and Thickness
Factors such as laser power and pulse shaping will be decided by the aluminum alloy grade, properties, and material thickness range that must be welded. Some alloys, such as 6061 and 2024, are heat-treatable and could require pulse shaping to avoid compromising strength.
Production Volumes and Throughput
What part or weld do you require to create in one hour, or how often do you need to weld? The comparative laser welder speeds and duty cycles can also vary significantly. Fully automatic welders may be used for high-volume production, while low-volume production may use benchtop manual welders.
Weld Quality Needs
They include cosmetic appearance, internal voids/porosity, bead shape, sheer strength, leakproofness, and post-weld finishing. Determine what quality characteristics should be assessed, how testing will be conducted, and what levels of deviation can be tolerated.
Budget
There is an indication that laser welding systems for aluminum can cost as little as $10,000 or more than $500,000, and this depends on the factors mentioned above, such as automation, weld quality, duty cycle, and power output. Set realistic budget expectations.
The most common methods in laser welding of aluminum are:
There are three main laser processes suitable for welding aluminum: There are three main laser processes ideal for welding aluminum:
Pulsed Nd: YAG Laser Welding
Pulsed solid-state Nd: YAG lasers with a 1. 06-micron wavelengths are widely used for welding aluminum materials, particularly when welding thin joints or heat-sensitive aluminum alloys. They can be run either in continuous seam welding or spot welding modes. Pulsing the beam can aid in controlling the heat input, which is an essential goal when welding. Fiber-delivered diode lasers are also emerging as a popular option.
This paper focuses on the Continuous Wave CO2 Laser Welding.
CO2 lasers of 10. 6-micron wavelengths can operate continuously for faster welds. Aluminum’s conductivity and reflectivity mean that welds demand higher power than steels. This makes CO2 welding suitable for thicker aluminum Welds above 3 mm.
Green Wavelength Diode Laser Welding
New affordable Diode lasers illuminate visible green light in the 515- 532 nm range for aluminum welding. Reflective aluminum reflects Green wavelengths more efficiently than infrared wavelengths, which are 2 to 3 times more absorptive. This facilitates faster speed welding than infrared lasers when the same power is applied.
h2. Factors to Consider When Purchasing Laser Welding Equipment
When investing in laser welding for aluminum, you’ll need to evaluate options across various equipment components: When investing in laser welding for aluminum, you’ll need to assess options across various equipment components:
Laser Oscillator
The laser oscillator produces the primary beam of laser light. As outlined above, common technologies include fiber, pulsed Nd: YAG lasers, CO2 lasers, and green diode laser oscillators. Consider wavelength, peak power, and pulse parameters.
Beam Delivery
How will the laser beam be transported from the oscillator to the welding area? Choices available for ownership include galvo scanning heads, robot mounting, and fixed optics, which should be sufficient for your working environment.
Motion System
The slides or tables that move the laser beam, part, or join area respectively require high precision. These can be multi-axis robot arms or linear or rotary stages.
Fume Extraction
Aluminum welding results in the formation of toxic gases, which require industrial fume removal arms positioned near the weld. Make sure the system is rated for aluminum fumes.
Monitoring and Controls
Controlling production and attaining repeatable welds need sensors, monitoring software, controls, and user interfaces. This includes simple systems where machines are connected to interfaces and more complex systems connected to the internet and can employ artificial intelligence to monitor performance.
Frame and Enclosures
Laser welding applications need sturdy and stable supporting structures such as tables, carts, and protective enclosures. The installation space should be adequate in size, easily accessible, and provide proper ventilation and isolation.
Increasing Quality and Enhancing Your Aluminum Laser Welds
Adhering to proper procedures and techniques is vital for achieving void-free, strongly-bonded, and visually acceptable aluminum laser welds: Adhering to appropriate procedures and methods is vital for attaining void-free, strongly-bonded, and visually acceptable aluminum laser welds:
Joint Design
Ensure the joint designs enable easy access to the laser welding area, fume removal, accommodation of mismatch and grinding, and the testing area. Avoid tiny gap variations.
Surface Preparation
Specifically, the aluminum surface oxides along the edges of the weld seam must be mechanically abraded immediately before welding. This prevents the unwanted materials on the electrodes’ surface from’ drossing’ the molten weld pool.
Beam Focusing & Indexing
More specifically, it targets or aims the laser to deliver the highest energy density possible on the joint line. This avoids detrimental HAZ softening, porosity, and undersized welds.
Pulse Tailoring & Heat Control
Using proper power density, pulse duration, laser pulse separation and the type of laser pulse profile ensures controlled heating and cooling as well as prevents crack formation due to hot cracking depending on the thickness of the material being worked on.
Fixtures and Jigs
Proper fixturing enables alignment of joints, penetrates the required depth of weld, corrects for gap differences due to fit up and avoids melting through of the base material.
Testing and Inspection
Non-destructive and destructive testing confirm the internal quality based on the acceptance quality level. The methods that are often used for the examination of aluminum laser welds include dye penetrant testing, X-ray testing, optical microscopy, peel/bend tests, and cross-sectioning.
Parameter Development
View more about adjusting parameters such as speed, beam angles, focus, and pulse shaping knobs at their best. While the creation of parameters may require time and effort, it is essential to achieving higher standards of quality and efficiency.
The use of laser welding on aluminum offers advantages compared to the conventional fusion welding methods in terms of accuracy and appearance, minimal distortion and ultimately lower cost over the life cycle. Therefore, by grasping the points discussed in this paper, buyers will be in a position to choose the right aluminum laser welding equipment and procedures for top notch quality welds, maximum throughput, and durability of the components and final products.